What Is Cost of Quality (COQ)?
The cost of quality (COQ) is the sum of all costs incurred in the design, development, manufacture, distribution, and sale of a product that is related to ensuring product conformance. On the other hand, the cost of poor quality (COPQ) is the sum of costs a company incurs to manage and correct failures found in its production processes.
COQ is also a methodology for measuring the amount of an organization’s resources that are used for defect prevention and ensuring product quality against the organization’s cost of failure. Adopting this methodology leads to fewer product defects—therefore also fewer product inspections—and facilitates a problem-prevention mindset throughout the manufacturing organization. Overall, the COQ mentality promotes a unifying culture that centers on reducing costs through improved product quality.
Why Is Knowing the COQ Important?
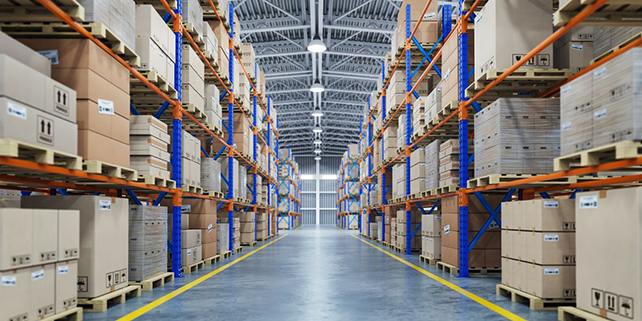
Knowing the cost of quality at your manufacturing organization is essential to understanding your overall bottom line. Product quality dictates how well your product sells, how loyal your customers will be to your organization, how many times your product is made with defects, and more. From start to finish, your manufacturing business is only as good as the quality of its products!</p><p>Let’s look at it from the perspective of these questions:
How much higher would your company’s profitability be if you were able to reduce your rework by just 10%?
How different would your manufacturing organization’s profitability be if you were able to reduce price adjustments due to process problems in half?
What would your revenue stream look like if you lost one or two big-ticket customers?</p><p>Defects are expensive in both obvious and subtle ways; on the surface, e.g. a product might incur additional production, inspection and processing costs due to aesthetic or functional defects, time to replace the parts, and process the RMA for the customer.
But upon deeper investigation, that same product might be costing the manufacturer in largely unseen ways like additional freight costs, administrative processing time, extra inspection, reworking and re-testing the product, and more. These costs might seem subtle or infrequent enough to be ignored at first but can have significant cumulative effects on your manufacturing company.
Four Major Cost Tracking Categories
When determining which costs to track in relation to quality, consider these:
Prevention Costs
These are the costs incurred in order to prevent defects and production failures. This might include the cost associated with quality planning, product specifications, design reviews, employee training, and more. What steps is your manufacturing company taking in order to prevent product defects?
Appraisal Costs
This factor is the cost to evaluate if your product meets established quality standards, such as those from your customer or other regulatory agencies. These costs might include product inspection, product testing labs, auditing process controls, preventative maintenance, supplier development, and more.
Internal Failure Costs
Internal failure costs can be broken down into five components:
- Scrap: Defective product or material that can’t be repaired or sold
- Waste: Additional paperwork, extra inventory due to poor organization, etc.
- The cost of reworking, sorting, and retesting products to fix errors
- Machine breakdowns
- Corrective action costs associated with failure analysis and the investigation of causes of product or process failures
Basically, this category of cost addresses which internal processes are leading to defective products or lessened quality.
External Failure Costs
Unlike internal failure costs, external failures are those that result from poor quality making it into the field such as service and repair costs, warranty claims, shipping damage that affects products, incorrect sales orders, and more.
How KPIs Support the COQ
KPIs (Key Process Indicators) are the essential metrics to help companies determine if they are achieving their goals in "key areas" such as expected process outputs, costs, resources consumed, quality, delivery timeliness, and safety. The measurement must always be expressed over time and compared against a plan or goal in order to maintain consistency and objectivity.
When it comes to addressing the COQ within your manufacturing organization, KPIs that aren’t hitting their goals are your best points of improvement. Measure the success of your efforts to reduce defects, rework, and cycle time in order to see the impact that quality has on your organization. Be sure that your metrics are always in a positive light - for improvement and not punishment—your goal is to use KPIs to develop a culture that is intensely oriented toward cost reduction and process improvement, which benefits everyone involved.
COQ Strategy for Success
The COQ strategy for success is only as impactful on your manufacturing business as the people who are striving to bring it to fruition. The foundational step to success here is to establish improving as an integral part of your business.
Follow this suggested flowchart when creating your own manufacturing company’s COQ strategy:
- Flowchart your company’s key processes
- Identify weak spots as financial opportunities
- Create small teams for each major opportunity
- Teams track cost data to highlight project impact from start to finish
- Teams meet weekly to work through these opportunities
- Teams perform root cause and corrective action analysis
- Projects may continue for weeks or even months
- Teams report on progress, which is celebrated no matter how small
- A problem-solving culture is facilitated at your manufacturing business
- Select the next set of projects and repeat!
Leveraging the cost of quality at your manufacturing company in order to improve your operations and bottom line is a great way to strengthen your team and thrive in this competitive market.